Penske Technology Group Enables Motorsport Teams to Improve Vehicle Performance
"The services we offer have become a crucial aspect of vehicle development for professional-level motorsport teams. That is in large part because we can offer flexible analysis tools based on MathWorks products."
Challenge
Solution
Results
- Reduced development time by more than 50%
- Increased offline testing
- Streamlined development
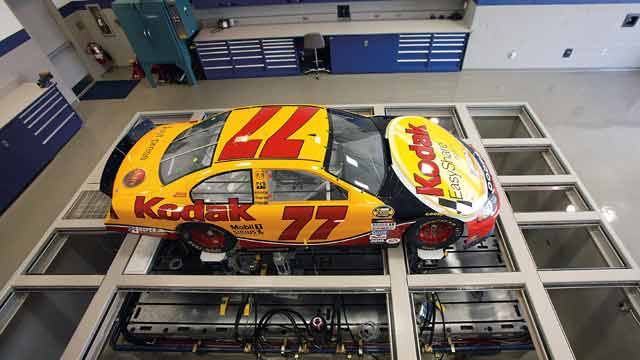
Penske Technology Group (PTG) receives varying requests from motorsport teams to more accurately predict vehicle performance before racing events. To meet the demand, PTG offers a dynamic shaker rig and analysis services based on MathWorks tools to determine the appropriate adjustments to damping characteristics that improve racecar performance.
"We see three to five teams per week—each with slightly different requests. We need analysis software that enables us to reuse our work and reduce development time," says Tom Sweetland, lead engineer at PTG. "MathWorks tools enable us to solve our customers’ problems without spending half the day writing code, while simplifying data analysis and dedicating more time to testing."
Challenge
PTG needed to find optimal damping characteristics of cars on its test rig to improve vehicle performance. To satisfy concurrent customer requests, PTG also needed to develop flexible analysis tools with an easy-to-learn programming language that included graphics and GUI-building capabilities. Moreover, because its shaker rig is in constant use, PTG sought to perform tests via computer simulations.
Finally, PTG required an analysis environment that could handle the logging of millions of data points as well as offer deployment capabilities for distributing analysis tools to its customers for further testing.
Solution
PTG uses MathWorks tools to analyze track, shaker rig, and simulated data as well as to deploy its tools to customers for further testing.
PTG’s shaker rig includes seven hydraulic actuators, four for road simulation and three that connect to the body of the car to simulate banking, cornering, and aerodynamic loads. “Our shaker rig is a tool for teams to tune vehicle dynamics for their car by adjusting spring and shock parameters,” Sweetland explains. “It’s based on finding the right damping characteristics for a car and investigating how a car will respond when it’s on a track.”
Customers provide recorded track data that measures damper displacement and hub acceleration. PTG engineers bring this data into MATLAB® and use preprocessing tools developed in MATLAB to extract the required data before filtering or resampling the data. The car is installed on the rig and this data is used to develop actuator loads and displacements that recreate the track data.
During shaker rig testing, the engineers use tools developed with MATLAB to analyze and display data in time and frequency domains. They adjust damping parameters of basic car models generated in Simulink® and Deep Learning Toolbox™ until the model simulations match up with the test data. They then use Optimization Toolbox™ with Simulink Design Optimization™ to optimize parameters to obtain the best track performance.
“Developing our applications with MATLAB is very quick,” says Sweetland. “We can concentrate on designing the interface rather than coding and implementing it. We log more than 600 million data points per test day, which are all analyzed with our MATLAB tools.”
Engineers use MATLAB Compiler™ to provide racing teams with tools for further analysis of shaker rig and simulation data. They also use these tools to analyze track test data.
PTG also uses Simulink to model aerodynamic loads that determine proper downforce loads for the actuators. They use Simulink Coder™ to automatically generate C code from the model, which is run in real time on the rig controller. This enables the rig actuators to respond correctly to changes in vehicle attitude.
They plan to use Simulink with Simscape Multibody™ to develop models of complete rig and car systems, enabling them to simulate full tests. “We want to try out new control routines on a virtual model of the rig and car to see how it performs without actually needing the rig and car available,” notes Sweetland. “This will be very beneficial because our facility is 100% booked.”
Results
Reduced development time by more than 50%. “Because MATLAB is an easy language to use, we spend most of our time getting the numbers to do what we want rather than programming,” says Sweetland. “Unlike other languages, MATLAB includes built-in debugging and plotting tools, so I don’t have to implement those from another source or write them myself, which would take two to four times longer.”
Increased offline testing. “Simulink enables us to simulate our tests on a virtual model,” says Sweetland. “This helps us optimize our damping characteristics and run more offline simulations, which allows us to make better use of test time on the rig.”
Streamlined development. “We do a lot of modeling in Simulink and Simscape Multibody,” notes Sweetland. “The integration between the analysis features of MATLAB and the modeling capabilities of Simulink helps us streamline our development.”