Medrad Ensures Safety of MRI Vascular Injection Pump
“MathWorks tools enabled us to understand the system-level interactions among the components, to model the physics, and to determine safety limits of the pump very efficiently and quickly.”
Challenge
Solution
Results
- Design time reduced by several months
- Prestigious industry award received
- FDA approval achieved
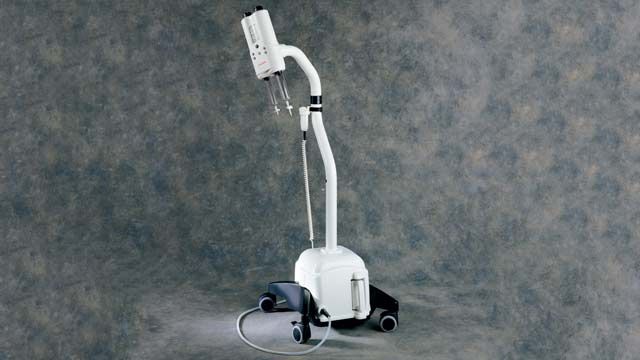
Vascular injection pumps developed by Medrad (now part of Bayer HealthCare) enable physicians to quickly detect arterial blockages, illuminate single blood vessels, and gauge the health of a beating heart using radiological or magnetic resonance (MR) imaging. The Medrad Spectris Solaris pump automatically injects contrast agents and saline solution into patients during MR imaging at flow rates up to 10 ml/sec and under pressures up to 325 psi. A precise amount must be injected to ensure patient safety and high image quality.
Using MathWorks tools and Model-Based Design, Medrad engineers predicted the pump’s pressure safety point without building costly hardware prototypes.
“Administering precise volumes of contrast agents is essential to our safety architecture,” explains John F. Kalafut, senior research scientist in Medrad’s Product Innovation and Advanced Development group. “MathWorks tools helped us make the appropriate decisions to ensure the design’s safety.”
Challenge
To predict the pump’s pressure safety point accurately, Medrad needed to improve the technology used to measure the pressure of the fluid delivered to the patient. Instead of relying on motor current as an indicator of fluid pressure, strain gauges would be used to improve pressure monitoring. In addition, because digital signal processors (DSPs) would be used as motor controllers, the effects of fixed-point mathematics for computing motor control signals would need to be evaluated.
To ensure safety and optimal performance, Medrad needed a complete understanding of how the pump’s pressure measurement system responded and functioned with other system components and the DSP motor controllers.
“We needed to understand how the different subsystems affected the fluid dynamics and the pressure generation of the unit,” says Kalafut.
Medrad also sought to augment and streamline the hardware testing required for FDA approval by using mathematical modeling and simulation.
Finally, Medrad engineers were required to reduce design times so that they could respond more quickly to competitive challenges.
Solution
The Medrad Spectris Solaris contrast injection system consists of several subsystems. Medrad used MathWorks tools to design the pump motor controller and the safety system.
“Model-Based Design enabled us to mathematically model each subsystem,” says Kalafut. “We are now able to understand the system behavior and determine how quickly pressure builds in the pump.”
Medrad used MATLAB®, Simulink®, and Control System Toolbox™ to define system requirements, quantify system performance, tune the motor control loop response, predict motor current draw, and determine battery life expectancy—long before the actual hardware was available or the software was written.
“With Simulink, you can demonstrate your system or subsystem model so that others can see and understand the relationships among the components,” says Kalafut.
During final testing, the design team discovered that radio frequency (RF) energy coupling into the strain gauges was causing unwanted shutdowns. Kalafut’s team used Signal Processing Toolbox™ and DSP System Toolbox™ to design and exhaustively simulate a more sophisticated filter to condition the signals.
“We made the original simple average filter more sophisticated using DSP System Toolbox and Signal Processing Toolbox, and shaved three weeks off the project in the process,” says Kalafut.
Medrad uses MathWorks tools throughout the company to reduce development time, improve product quality, and research new technologies and product innovations.
Another team responsible for a new cardiovascular injection system was able to define various system requirements using an existing Simulink model. “That’s where Model-Based Design and Simulink have many advantages over C and Fortran,” says Kalafut.
For their new patient monitoring system, Medrad is automatically creating the embedded software from Simulink block diagrams using Embedded Coder®.
Using Simulink Real-Time™, they also created a hardware-in-the-loop simulation of the vascular injection pump fluid dynamics and the human vascular system. This real-time simulation will enable Medrad to reduce the number of tests using real fluids (“wet testing”), which are typically required to validate pump controller designs.
Results
- Design time reduced by several months. “Simulink helped us to investigate and predict what the pressure safety point should be without ever building a piece of hardware or writing any software,” says Kalafut. “That saved us months in designing the pressure subsystem.”
- Prestigious industry award received. “Our rigorous quality standards, which we call Quality For Life®, apply from product conception through manufacturing and service, and resulted in us winning a Malcolm Baldridge National Quality Award,” says Kalafut. “Using MathWorks tools helps us in the design of high-quality products.”
- FDA approval achieved. “MathWorks tools helped us use mathematical modeling and simulation to rigorously demonstrate that we had designed a safe product,” Kalafut says.